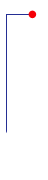 |
Audio Fluids
Designing With Ferrofluids
Proper selection of a ferrofluid requires a careful balance of
the properties of the ferrofluid vs. the properties of the loudspeaker.
The five most important factors to consider are quantity, viscosity,
magnetization, compatibility and volatility.
Quantity
The optimum quantity of ferrofluid for a loudspeaker
is determined by the physical dimensions of the air gap and can
be calculated with the use of the following formulae:
English
V [µl] = 56500 A [E2+C2-B2-D2]
(where A, B, C, D in inches) |
Metric
V [µl] = 3.5 A [E2+C2-B2-D2]
(where A, B, C, D in mm) |
|
where:
A= Top plate thickness
B= Radius of
pole
C= Inner radius
of voice coil
D= Outer radius
of voice coil
E= Inner radius
of top plate |
|
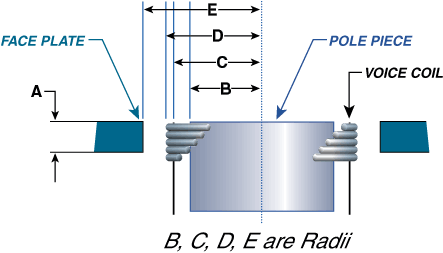 |
The recommended tolerance on ferrofluid quantity
is ±10% which is best maintained through the use of a positive
volume displacement dispenser. Maintaining the proper ferrofluid
quantity is critical as overfilling the gap is wasteful and can
lead to leakage while underfilling the gap minimizes the heat transfer
benefits of the ferrofluid, compromises the fluid's long term reliability
and can lead to response anomalies in the loudspeaker.
Viscosity
Once the ferrofluid amount has been determined,
the viscosity of the ferrofluid should then be selected with respect
to the desired amount of damping.
Magnetization
The magnetization value of the ferrofluid should
be balanced against the loudspeakers air gap flux density and voice
coil excursion.Tweeters or compression drivers having high air gap
flux and minimal coil excursion require ferrofluid magnetization
values in the 100-200 gauss (10-20 mT) range. Woofers, on the other
hand, typically have much lower air gap flux and much greater coil
excursion and require ferrofluid magnetization values in the 300-400
gauss (30-40 mT) range. High gauss ferrofluids generally have a
shorter life at high temperatures. To ensure long term reliability,
it is therefore recommended that only as much magnetic material
as needed is used.
Compatibility
Successful ferrofluid application engineering requires
that the ferrofluid be fully compatible with all the materials and
adhesives which have the potential to come into contact with the
ferrofluid including:
- Voice coil bobbin/former material: The
critical property here is that the material be non-absorbent which
eliminates kraft papers and uncoated Nomex® materials. Compatible
materials include aluminum, and Kapton®.
- Collar material: Again, the critical
property here is that the material be non-absorbent. Coated Nomex
and Kapton have all been used successfully in this application.
- Voice coil wire adhesive: All popular
methods (wet winding, self bonding) and related adhesives are
compatible with ferrofluids and no incompatibilities are known
to have been encountered. New techniques or adhesives should be
analyzed by Ferrofluidics Corporation to ensure their compatibility
with ferrofluid.
- Adhesive joints: The glue joint at the
bobbin/diaphragm or bobbin/cone/spider junction as well as the
magnet system structural adhesive must be compatible with ferrofluid.
Commonly used acrylics, epoxies and cyanacrylates are compatible
with virtually all hydrocarbon based fluids and most ester based
fluids. Ester based fluids should not be used in conjunction with
rubber based adhesives. When introducing ferrofluid into a design,
or in changing the adhesives used, compatibility should be fully
tested.
Avoiding fluid migration
Care should be taken to ensure that there are no
capillary paths present by which the ferrofluid could migrate from
the gap. The most common are:
- Machining grooves in the magnet top plate:
If these grooves terminate in the air gap, ferrofluid can travel
along the grooves via capillary action.
- Cotton impregnated lead wires: The cotton
can absorb the ferrofluid if they come into contact with each
other. This type of material should be wax coated if used in conjunction
with ferrofluid.
- Lead wire migration: Ferrofluid can travel
between the collar and former along the lead wires via capillary
action. This pathway can often be successfully sealed using a
wicking adhesive (such as Loctite 290) or a gel type adhesive
(Hernon's Quantum 134) which is draped over the lead wires before
the collar is applied.
- Bobbin slit migration: If the gap between
the two ends of the voice coil former is too narrow (< 0.001"
/ 0.025 mm) ferrofluid can travel up the slit via capillary action.
Volatility
The thermal capacity of the ferrofluid should be
chosen with respect to the operating temperatures of the voice coil.
Moderate to low temperature operation requires our more standard
products such as the APG 800 or APG 900 series Ferrofluids (hydrocarbon
based materials) while more demanding high temperature applications
should utilize the ester based APG "O" or "S"
series or the hydrocarbon based APG 2100 series.
Ferrofluid | Vacuum
Feedthroughs | Thermoelectric Modules
Contract Manufacturing | Literature
Rack | Specialty Seals
Inertia Dampers | Electron
Beam Evaporation
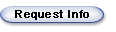 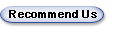
|