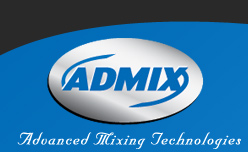
Powder Induction
NEW! Click here to watch our new Powder Induction Video
There are many types of applications requiring powders being fed into liquids, and some general categories follow. Minimizing air entrainment, increasing repeatability, improving operator ergonomics and eliminating waste are all challenges faced with traditional plant processes assembled from a variety of systems.
Admix, Inc. offers a range of products to resolve these issues. Our Optifeed utilizes a pump and eductor to entrain powders into a liquid stream, providing excellent product flow with minimal equipment. Tougher to disperse materials or those requiring high shear can be handled by our DynaShear with Fastfeed system, merging our knowledge of eductor performance and high shear in-line mixing for a simple-to-operate skid mounted unit. Our most unique product is called the VacuShear LiquiProcessor system, which incorporates a powder feed device, transfer system, vacuum rated blend tank and mixer for the maximum flexibility, fastest mixing times and shortest deaeration cycles. The VacuShear can be equipped with any mixer from our entire range of rotating batch equipment, for the ultimate in flexibility.
Dissolving - For simple wetting out of a powder or solid material that completely dissolves in water or other liquid, i.e. sugar, salt in less than saturation concentration. High shear is preferred and will always be faster and more efficient, low speed may be acceptable where mix time is not a factor.
-
Rotomixx - 350 to 1750 RPM (Low Shear)
-
Rotosolver - 1750 to 3600 RPM (High Shear)
-
Rotostat - 1750 to 3600 RPM (High Shear)
Batch Processing
VacuShear with one of the following mixers:
In-line, Recirculating Batch or Continuous Processing
Dispersing - Where powders or solids are introduced into a liquid at a rapid rate to insure a thorough distribuiton for a homogeneous product. Many powders can be dispersed to form a slurry where the mixed viscosity stays constant or can be followed by a hydration stage where viscosity may build. High shear is necessary for effective dispersion.
Batch Processing
VacuShear with one of the following mixers:
Rotosolver - 1750 to 3600 RPM (High Shear)
Rotostat - 1750 to 3600 RPM (High Shear)
In-line, Recirculating Batch or Continuous Processing
Boston Shearmill with Fastfeed - 3600 to 10,000 RPM (Very High Shear)
Emulsification - Typically involving immiscible liquids as in oil and water or adding powders to a liquid, and consisting of a continuous and a dispersed phase. An emulsifying or stabilizing agent (surfactant) may be needed for stability. Could produce very high viscosities. High shear is always recommended.
Batch Processing
VacuShear with one of the following mixers:
Rotosolver - 1750 to 3600 RPM (High Shear)
Rotostat - 1750 to 3600 RPM (High Shear)
In-line, Recirculating Batch or Continuous Processing
Boston Shearmill with Fastfeed - 3600 to 10,000 RPM (Very High Shear)
Hydration - Typically follows dispersion of a viscosity building gum or hydrocolloid. Once the gum is rapidly dispersed, hydration normally begins immediately and could take from seconds to several minutes. Examples include starches, soy, pectin, xanthan gum, CMC, etc.
Batch Processing
VacuShear with one of the following mixers:
Rotosolver - 1750 to 3600 RPM (High Shear)
Rotostat - 1750 to 3600 RPM (High Shear)
In-line, Recirculating Batch or Continuous Processing
Boston Shearmill with Fastfeed - 3600 to 10,000 RPM (Very High Shear)
Particle Size Reduction / Deagglomeration - Shear combined with physical impact causes particles or droplets to be reduced to smaller diameters. This is based on the tip speed and mechanical design of the shear head. High shear mixers manufactured by Admix will provide particle or droplet size reduction in the range of 0.5 to 5 microns, with better than 90% distribution under 3 microns.
Batch Processing
VacuShear with one of the following mixers:
Rotosolver - 1750 to 3600 RPM (High Shear)
Rotostat - 1750 to 3600 RPM (High Shear)
In-line, Recirculating Batch or Continuous Processing
Boston Shearmill with Fastfeed - 3600 to 10,000 RPM (Very High Shear)
CIP (Clean-in-Place) Applications
Most equipment manufactured by Admix is specifically designed to allow easy cleaning either manually or cleaned-in-place with spray balls or mechanical equipment. Our Rotosolver provides the ultimate in cleanability as there are no hidden crevices or surfaces.
3-A Symbol Authorization
Most equipment manufactured by Admix has been granted 3-A TPV Symbol Authorization and meets the requirements of the applicable Standards.
Rotosolver - Standard #73-01
Rotomixx - Standard #73-01
Boston Shearmill - Standard #36-01
DynaShear - Standard #36-01
Admixer - Standard #35-03