PTF
Material Performance and Reliability
Just because Polymer Thick
Film technology is low cost does not mean that it is low quality. With
Poly-Flex Circuits, it's just the opposite. Our materials formulated
by our Research and Development group are extensively tested for high
performance and reliability. Materials have been refined over years
of high volume production - the benefit of having manufacturing and
material development under the same roof. Batch to batch consistency
is ensured via our tightly controlled in-house mixing facility.
This section is intended
to give the reader greater appreciation for the reliability of Poly-Flex's
Polymer Thick Film circuits by understanding the reliability tests performed
on the materials. Unlike the copper based circuitry, there are few industry
standard methods and criteria for Polymer Thick Film (PTF) reliability
testing. Moreover, few PTF manufacturers perform reliability testing
to any significant extent. As a pioneer of PTF technology, Poly-Flex
Circuits takes reliability very seriously. Our inks and adhesives are
subjected to very aggressive accelerated aging tests. They must show
virtually no change from their original state - <20% change from
initial resistance value is a common criteria.
The tests described in this
section have been performed during our material qualification program.
Many of these test are also used as process controls in the material
mixing, printing or component assembly operations.
Silver
Inks
The test results described
below are for Poly-Flex's standard production silver filled ink.
Print
Quality
Poly-Flex inks are formulated
to run at very fast rates on our high speed production print presses.
This speed advantage translates to a cost advantage over printing inks
that are not tuned to high speed printing. Moreover, our inks are formulated
for long screen life to eliminate ink waste and unnecessary changeovers
due to ink drying. When formulating a new ink, our Research and Development
Chemists work with the production printers from conception through final
qualification. Circuits are fabricated at normal production printing
speeds over the course of a production shift. Samples taken at different
time intervals are visually inspected for print quality. Line definition
must be good with no pin holes observed on any of the samples. This
test is repeated with different ink batches and longer production runs
during the scale up phase.
Resistivity
Poly-Flex inks provide resistivity
from 10 to 20mOhms/square/mil. The ink resitivity is determined by measuring
the resistance and ink height on a standard 600 square test pattern.
Adhesion
and Abrasion Resistance to Untreated Polyester
Poly-Flex Circuits' printed
inks are formulated to provide excellent adhesion to untreated polyester,
eliminating the need for expensive print treatments required for inferior
inks. Our inks also demonstrate excellent surface hardness - a property
vital to a robust membrane switch. The tests described below are used
during ink formulation as well as process controls for ink mixing and
production printing.
Adhesion, ASTM D 3359
A standard test pattern
(square block) of silver ink is printed and cured on untreated polyester.
A cross hatch (knife blade) is used to cut through the ink. A tape is
then placed over the cut area, allowed to stand for 60 seconds and then
pulled off. The samples are then examined for any missing pieces of
printed ink. All samples must exhibit 100% adhesion.
Abrasion, ASTM D 3363
This method is used to determine
the pencil hardness equivalent of the ink. A Paul Gardner test apparatus
is used to ensure repeatability of the results. Typically, this test
can vary by +/- 1 hardness grade. A minimum hardness of 2H is required.
Standard inks measure 3H to 4H.
Adhesion
and Resistivity Over Dielectric
Some product applications
require conductive crossover traces. Standard 600 square test samples
were printed over Poly-Flex's dielectrics. Adhesion and resistivity
were tested per the methods described above. Adhesion was 100% in all
cases. Resistivity was within 10% of the ink-on-polyester value.
Crease
Resistance
This test was used to determine
the change in resistance of a conductive ink circuit trace after a crease
in both tension and compression. Samples were printed on 0.005 inch
(125um) polyester using a standard 600 square serpentine pattern. The
samples were folded and a 500g weight was placed at the fold for 60
seconds. Resistance measurements were taken prior to testing and 15
seconds after removal of the 500g weight. The change in resistance was
less than 10%. Test samples were visually examined under 30X magnification
with no evidence of cracking or delamination.
Repeated
Flex, UL 746E
The purpose of this test
was to determine the durability of a conductive ink trace (with and
without a cover coat dielectric) when flexed 180 degrees around a 1/8"
(3mm) mandrel. The test sample is flexed so that the conductive ink
is in tension or compression. The test samples were subjected to 50
cycles. The data is reported as the average percent increase in resistance
of the samples. Without dielectric, the resistance increased less than
7%; with dielectric, less than 12%. Test samples were visually examined
under 30X magnification with no evidence of cracking or delamination.
Accelerated
Aging Tests
The purpose of this test
was to determine the performance of conductive ink when subjected to
specific accelerated tests that simulate product aging, shipping and
storage environments.
Thermal Shock
Thermal Shock was performed
per MIL-STD-1344, Method 1003, 25 cycles, -55C to +85C, 30 minute soak
at each extreme, less than a 5 minute transfer time between temperature
extremes. This test simulates the thermal excursions that may be seen
during shipping or actual usage for some products. 600 square serpentine
coupons were used for this test.
High Temperature Aging
The test was performed per
MIL-STD-202, Method 108A, +85C for 500 hours, less than 20% humidity.
This condition simulates long term application in high temperature storage
conditions. 600 square serpentine coupons were used for this test.
Accelerated
Aging Test Results
Test
|
Conditions
|
Duration
|
% Resistance Change From Initial Value
|
Thermal Shock
|
-55C/+85C, 30 min soak, <5min transfer
|
25 cycles
|
-7%
|
High Temperature Aging
|
+85C
|
500 hours
|
-5%
|
High Temperature / Humidity
This test simulates long
term application in high humidity environments. It is run in conjunction
with the Poly-Solder® conductive adhesive. Tests were conducted
for 1000 hours each at the following conditions: 60C/90%RH, 70C/85RH,
85C/85RH. The junction resistance of components mounted with Poly-Solder
® was monitored. All samples passed the criteria of less than 20%
increase in junction resistance over the 1000 hours. See the Component
Attachment Section for further details.
Pre-Aging
Flex Test
The purpose of this test
was to determine the durability of a conductive ink trace (with and
without a cover coat dielectric) after being subjected to the thermal
shock and high temperature aging tests described above. Following the
aging tests, samples were flexed 180 degrees around a 1/8" (3mm)
diameter mandrel, both in tension and compression. Test samples were
subjected to 50 cycles. The results, expressed as percent increase in
resistance, are as follows:
Condition
|
Compression
|
Tension
|
Thermal Shock, no dielectric
|
8%
|
11%
|
Thermal Shock, with dielectric
|
8%
|
9%
|
High Temp Aging, no dielectric
|
4%
|
7%
|
SMT
Component Attachment (Poly-Solder® and PF200)
Poly-Flex attaches Surface
Mount Technology (SMT) components to flexible circuits using its patented
Poly-Solder® Isotropic Conductive Adhesive. After curing of Poly-Solder®,
the PF200 mechanical strain relief encapsulant is applied to permit
extreme circuit flexing without degradation of the component junctions.
Poly-Solder® was specifically
formulated to form stable junctions to standard SMT components, even
in very humid environments, without special metalization. It is this
patented high temperature / humidity performance that differentiates
Poly-Solder® from inferior conductive adhesives. Its reliability
has been proven over many years of testing and high volume production.
Over 75 million components per year
have been attached using Poly-Solder®.
Die Shear
Strength, MIL-STD-883, Method 2019.5
The adhesion strength is
tested by applying a force laterally to a component (that has been mounted
with Poly-Solder ®) until it is sheared from the substrate. Both
a lab scale / material control test and a production process control
test have been established. Both tests are performed without the PF200
mechanical strain relief material applied.
Production Test:
A corresponding production process control test uses a chip component
(resistor, LED or capacitor) placed into stenciled conductive adhesive
pads on polyester. Off-the-shelf components with standard Pb metalization
are used. Adhesion values correlate to component package size and lead
type:
Package Style
|
Lead Style
|
Package Size
|
Average
Adhesion (lbs)
|
Chip Component
|
Formed Metalization
|
0603
|
5.5
|
Chip Component
|
Formed Metalization
|
0805
|
7.0
|
Chip Component
|
Formed Metalization
|
1206
|
8.0
|
1206 LED
|
Gull wing
|
1206
|
7.0
|
High
Temperature / Humidity
This test simulates long
term application in high humidity environments. In order to monitor
the component junction resistance, a daisy chain test vehicle was developed.
This circuit incorporated 10 zero ohm resistors connected in series,
a daisy chain PLCC44 (50 mil pitch) and a daisy chain QFP80 (25 mil
pitch)
Poly-Solder® was tested
with and without PF200. The test circuit pattern was printed on 5 mil
(125um) polyester using Poly-Flex's silver ink. The conductive adhesive
was stenciled on the polyester and the SMT components attached. PF200
was applied to half the circuits. The series chain resistance for each
component type was monitored during exposure to high temperature and
humidity using a four wire measurement technique. The pass/fail criteria
was less than 20% increase in junction resistance over 1000 hours exposure.
Results are as follows.
Test Conditions
|
Without PF200
|
With PF200
|
60C, 90%RH, 1000 hrs
|
100% Pass
|
100% Pass
|
75C, 85% RH, 1000 hrs
|
100% Pass
|
100% Pass
|
85C, 85%RH, 1000 hrs
|
100% Pass
|
100% Pass
|
Poly-Solder was then tested
against two commercially available conductive adhesives, without PF
200. Both commercial materials shorted on the QFP80 component due to
poor material printability. Poly-Solder® did not exhibit short circuit
conditions as it was developed for fine pitch printing applications.
The test circuits were exposed to 85C, 85%RH. Results were as follows:
Material
|
Resistors
|
PLCC44
|
QFP80
|
Conductive Adhesive A
|
Failed <96hrs
|
Failed<96hrs
|
N/A (shorted)
|
Conductive Adhesive B
|
Failed <240hrs
|
Failed <300hrs
|
N/A (shorted)
|
Polysolder®
|
Passed >1000 hrs
|
Passed >1000hrs
|
Passed >1000hrs
|
Numerous third party studies
have also concluded that Poly-Solder® has much better temperature
and humidity performance than other commercially available materials.
Accelerated
Aging with Flexural Stress
This test simulates the
flex stress a circuit may see during handling or end application. The
test vehicle was a functional circuit containing two LED's and two resistors,
mounted with Poly-Solder ® and encapsulated with PF200 strain relief
material. These circuits were wrapped around a 0.5 inch (12.5mm) diameter
mandrel to apply stress to the component area. Circuits were functionally
tested and then subjected to the tests listed below. The circuits were
functionally tested after environmental exposure.
Test
|
Conditions
|
Duration
|
Results
|
Thermal Shock
|
-50C/+85C, 30 min soak, < 5 min transfer
|
25 cycles
|
100% Pass
|
High Temperature & Humidity
|
+75C/85%RH
|
1000 hours
|
100% Pass
|
Thermal Cycle
|
-50C/+85C, 12 hr soak, <30 min transfer
|
40cycles hours
|
1000% Pass
|
Flip
Chip
Poly-Solder® has also
been qualified for Flip Chip die attachment. A Flip Chip test vehicle
was developed similar to the SMT circuit described above. The FB250
die from Flip Chip Technologies was selected as the test die, and a
corresponding circuit was designed. This die is 0.250" per side
with 48 SnPb bumps on 20 mil pitch.
The die were placed into
printed Poly-Solder® and cured. Underfill was then dispensed and
cured. The circuits were exposed to 1000 hrs 85C/85%RH and 250 cycles
of Thermal Shock (-55C/+85C, 30 min soak, 10 second transition). Results
are as follows:
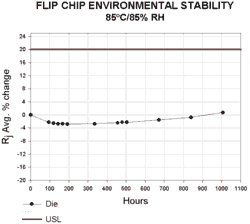 |
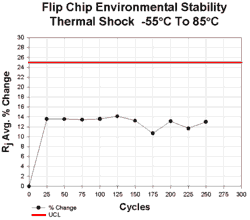 |
Graph
1
|
Graph
2
|
Dielectric
Materials
General
Dielectric materials provide
mechanical protection of conductive traces, electrical isolation of
adjacent conductors and electrical insulation between conductive layers.
While most polymer dielectric can provide some degree of mechanical
protection, their isolation and insulation properties are most critical
to the long-term reliability of circuits with silver conductive traces,
in high temperature/ humidity environments.
High temperature and humidity
with an electrical bias has become a generally accepted standard for
product life and reliability growth testing. Failure mechanisms, such
as corrosion and ion mobility, can be triggered by the effects of these
conditions. This testing was used by our research chemists to develop
(and make improvements) to PF114 "hydrophobic" dielectric
for telecommunication and appliance applications.
Insulation
Resistance Testing
Case
1 - Sample circuits were produced with Poly-Flex PF012 silver
and PF114 dielectric inks, and with similar materials from a commercial
manufacturer. The separation between conductors on the samples was .015"
at their closest point. The circuits were sent to an independent lab
to perform 70ºC and 85%RH 1000 hour testing with a 10 VDC bias between
adjacent conductors. A leakage current of >20uA was considered a
failure.
Circuits with the commercial
dielectric coating exhibited a steady increase of leakage current until
exceeding the 20uA limit at 400 hours. The circuits exhibited severe
discoloration with evidence of electromigration (dendritic growth.)
The circuits manufactured
with Poly-Flex materials continued to 1000 hours with a minimal increase
of leakage current. When removed from the environmental chamber the
circuits showed little discoloration and no evidence of electromigration.
Case
2 - A manufacturer
of appliances subjected flex circuits manufactured by Poly-Flex to the
following temperature/ humidity sequence for a total of 1000 hours with
a 20VDC bias:
TEMP.
|
HUMIDITY
|
SOAK
|
+70 º C
|
50% RH
|
2 HOURS
|
+45 º C
|
98% RH
|
2 HOURS
|
+85 º C
|
85% RH
|
2 HOURS
|
+25 º C
|
35% RH
|
2 HOURS
|
All test samples passed
functionality requirements at the conclusion of the accelerated testing.
Some water residue was present on the samples, but no dendritic growth
was evident.
Isolation
Resistance Testing
The following graph shows
the results of high temperature immersion testing of a commercially
available dielectric material vs. the standard PF114 dielectric in production
today, and improved versions of PF114 that will be released into production
this year. Each test sample contained 400 cross over points. This extreme
test (developed by PFC) allowed our chemists to quickly determine the
effect of formula modifications.
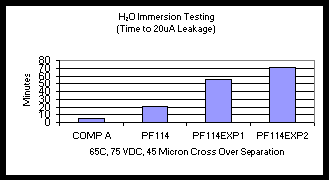
The following graph shows
the effects of both temperature and voltage acceleration factors on
polymer thick film materials using 400 cross point test samples. These
data were helpful in predicting long-term product reliability, and provided
a base line for materials improvement.
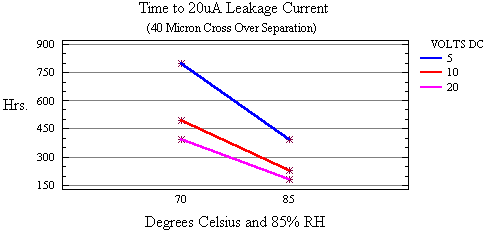
Other White Papers
Tactile Polyester
Dome
Flip Chip