business > medical coating
|
ParyLAST |
Plasma Enhanced Parylene Coating |
 |
ParyLAST coatings are |
 |
Conformal: |
 |
ParyLAST is a tough, pin-hole free coating applicable over any complex geometry. |
 |
Chemically inert: |
 |
ParyLAST has superior chemical resistance to nearly all known solvents. |
 |
Tenaciously bonded: |
 |
AST's patented parylene processing techniques (U.S. Patent Nos. 5,355,832 and 5,447,799) assure superior bonding to plastics, glasses, and metals as compared to that of conventional parylene processing. |
 |
Accepted: |
 |
ParyLAST has a long history of use and can be found in a number of FDA approved implantable devices. |
 |
Biocompatible: |
 |
ParyLAST has demonstrated biocompatibility in long and short-term tests. |
 |
Environmentally sound: |
 |
The ParyLAST process is a dry process with no chemical waste or residual solvent concerns. |
Insulating: |
 |
ParLAST has exceptionally high dielectric strength and is thus suitable as an insulating material in medical products. |
 |
 |
|
 |
 |
 |
How is ParyLAST different from conventional parylene? |
 |
In conventional parylene deposition, parts are first cleaned. Often this cleaning is done with a degreasing solvent. Next, they are soaked in adhesion promoters to improve the inherently poor adhesion of parylene. Lastly, the parylene is vapor deposited on the parts in a vacuum chamber.
ParyLAST overcomes parylene's adhesion limitations by creating molecular level binding between the substrate and the parylene coating. This is achieved by the integration of plasma cleaning and vapor deposition. When parts are to be treated with ParyLAST, they are placed into the patented reactor. First, they are cleaned and surface activated via a gas plasma molecular activation surface treatment. Then, without breaking containment, parylene is deposited on the surface via the standard vapor-polymerization process. The resulting ParyLAST coating, while chemically identical to conventionally applied parylene, is unlike it in that it is a coating with a lifetime resistance to delamination and minimized component failure due to liquid propagation into the coating/substrate interface. |
|
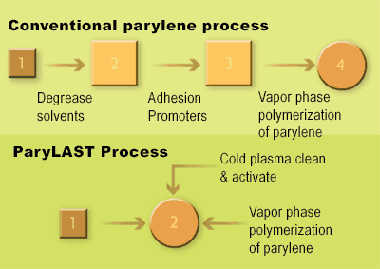 |
 |
|
Chemical Resistance |
 |
All values are in cm3-mil/100 in2-24hr-atm at 23 C |
 |
Nitrogen |
0.95 |
Oxygen |
7.10 |
Carbon Dioxide |
7.70 |
Hydrogen Sulfide |
13.00 |
Sulfur Dioxide |
11.00 |
Chlorine |
0.35 |
Moisture |
0.14 cm3-mil/100 in2-24hr-atm at 37 C 90%RH |
|
 |
Saline Soak Test |
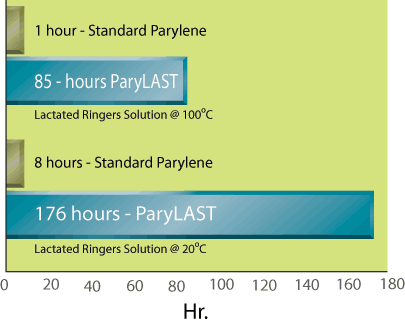 |
 |
Tenacious Bonding |
 |
Method:ASTM D3359-95a "Tape test" |
 |
Coating is cut into an "X" or into a crosshatch pattern per protocol. The coating is covered with #810 Scotch Tape and then the tape is pulled off. The degree of coating damage is qualitatively assessed. 0 means removal of the coating beyond the cut area while 5 means no peeling or removal. Intermediate numbers refer to results between these two extremes. From the data, ParyLAST clearly demonstrates superior adhesion. |
 |
Cutting Pattern |
 |
|
X-Cut pattern |
Cross-Hatch Pattern |
 |
Adhesion Rating |
 |
Conventional Parylene | ParyLAST |
 |
0(10 measurements) | 5(31 measurements) |
0(16 measurements) | 5(16 measurements) |
|
|
 |
Biocompatibility and Sterilization |
 |
ParyLAST can be sterilized via ETO, gamma radiation, or e-beam sterilization. |
 |
ParyLAST has passed the following biocompatibility tests: |
 |
- Intracutaneous reactivity
- Muscle implantation (14 days and 6 months)
- Systemic toxicity
- Cytotoxicity
- Sub-chronic toxicity
- Hemocompatibility
- Ames mutagenicity
|
 |
Electrical Insulation Properties |
 |
Dielectric strength, short time (Volts/mil, @ 1 mil) |
6800.00 |
 |
Volume resistivity, 23 C, 50% RH (Ohm-cm) |
6.0E+16 |
Surface resistivity, 23 C, 50% RH (Ohm) |
1.0E+15 |
Dielectric constant, 60 Hz |
3.15 |
Dielectric constant, 1000 Hz |
3.12 |
Dissipation factor, 60 Hz |
0.02 |
Dissipation factor, 1000 Hz |
0.02 |
Dissipation factor, 1,000,000 Hz |
0.01 |
 |
|