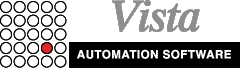
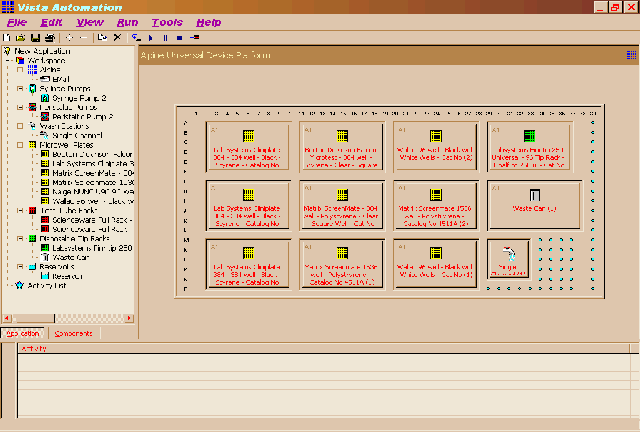
CLICK IMAGE FOR EXPLODED VIEW
Vista
software completely automates the set-up and operation of the
and
liquid handling automation systems. Researchers and technicians
can easily run archived applications or create new applications
with a minimum of effort or training. This application-focused software
uses a Graphical User Interface that employs ordinary commands such
as "Select" and "Drag-and-Drop". First time
users are amazed at how little time it takes to set up and run an
application.
CLICK
IMAGE FOR EXPLODED VIEW
Running
an Application from the User's Archives
The user opens the Application Browser with the mouse and selects
the appropriate application. A pictorial representation of a numbered
and "gridded" work deck, known as the Universal Device
Platform (UDP), appears on the screen. The user follows this pictorial
guide to position reagent containers, rinse stations, microplates,
disposable tip racks, and all other devices on the Universal Device
Platform. The user then simply selects "Run" to start
the application. To change applications, the user chooses another
application from the Application Browser and proceeds as above.
Setting
up a New Application
The user sets up a new application on an
or
liquid handling automation system in just five steps..
1.
Select the peripherals needed in the application from the user's
inventory of pumps, rinse stations, probes, and other devices.
2.
Select the types of sample formats and containers: 96, 384, and
1536 microwell plates, test tube racks, vial racks, beaker racks,
etc.
3.
Move plates, racks, and rinse stations with the "Drag and
Drop" command onto a "snap-to-grid" image of the
Universal Device Platform. Vista software
manages the dimensions and tolerances associated with these placements.
4.
Put together the sequence and timing of robotic movements and
the control commands for the pumps and other devices required
in the application. This is done by first selecting a microwell,
test tube, rinse station, or other device location, clicking on
a peripheral such as a pump, and then setting the peripheral's
operating parameters such as dispensed or aspirated volume, rate
of dispensing or aspiration, etc. A record of robotic movements
and device tasks is automatically stored and displayed in the
Activity List section of the screen.
5.
Name the application and archive it in the Application Browser.
The physical layout on the Universal Device Platform as well as
the sequence and timing of all robotic steps are stored with the
application.
<back
to top>
|